Thermoplastic composites may become the "shoulder" in the aviation industry, and the six applications are the first to see
Utpe elastomer portal, cutting-edge materials, carbon materials technology, xianji.com/xing Xiuyan / 2022-05-26 14:53:35 79250
With the continuous exploration of materials, the market demand for thermoplastic composites is growing rapidly. ACMA has set up a composite growth group to promote and publicize thermoplastic composites to end users and thermosetting composite manufacturers, so as to make thermoplastic composites have more markets.
At the time of setting off the trend of thermoplastic composites abroad, the application of high-performance thermoplastic composites in the domestic market is still in a "placid" state, and neither the manufacturer nor the customer seems to have officially entered the state.
However, the application technology of thermoplastic composites in the aviation industry has been implemented.
Recently, we are delighted to welcome the successful completion of the first flight test of the first C919 large aircraft! It is reported that in the "skin" of C919, the consumption of the third generation aluminum lithium alloy materials and advanced composite materials reached 8.8% and 12% respectively. Compared with the "competitors" of Boeing 737 and Airbus A320, the C919 uses more advanced composite materials.
The birth of C919 marks that domestic large aircraft will soon enter the era of commercial operation. Let's look forward to the official delivery of domestic large aircraft, but also have more expectations for the application of advanced composite materials in aerospace.
Today, let's take a look at the outlook of international experts on the future application of thermoplastic composites in the aviation industry:
According to the 2022 issue on the website of spiritaerosystems, when you look at an airplane, what do you think of first? Advanced aviation equipment is a "time capsule", which carries the great ideas of a generation. So, when looking into the future of flight, what are the characteristics of this era that people hope the next generation of aircraft can show? Lighter, faster and more sustainable must be pursued continuously. The use of advanced structural thermoplastic composites is a solution for the new generation of aviation equipment to obtain these characteristics. However, due to the lack of appropriate equipment, opportunities and R & D priorities, thermoplastic composites can not give full play to their potential in the whole industry.
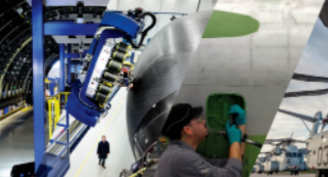
The development of next generation manufacturing processes, such as automatic forming, material placement and welding, must be industrialized so that thermoplastic composites can be widely used in large-scale aerospace manufacturing.
So why are thermoplastic composites important in aerospace? How will thermoplastic composites support the development of the next generation aircraft? How can the properties of thermoplastic composites meet the project requirements? What are the practical applications of advanced thermoplastic composites?
Why are thermoplastic composites important in aerospace?
Traditional metals such as aluminum and steel account for 70% of the materials used in aircraft manufacturing. However, the market demand for lighter and more efficient aircraft is increasing. In terms of thermosetting composites to reduce aircraft weight, researchers have rich professional knowledge. With the development of the industry, thermoplastic composites have gradually become the focus of research. Both types of materials use the high specific stiffness and strength of carbon fiber reinforced polymers to design lighter, higher strength aircraft.
At present, thermoplastic composites are replacing traditional materials in various applications, usually used in smaller parts. When thermoplastic composites are used in large components, such as longitudinal beams, frames, bulkheads and fuselage skin panels, the weight reduction effect of aviation equipment will be very significant, and the whole industry will also benefit greatly. Split's goal is to mature the use of thermoplastic composites in areas where automated high-speed manufacturing can be achieved, which means that the melting, forming and curing processes can be repeated in a very short period of time.
How will thermoplastic composites support the development of the next generation aircraft?
Thermoplastic composites have been clearly applied in three key fields: new generation conventional aircraft, consumable aircraft, urban air traffic (UAM) aircraft and other emerging markets. Light and high-performance aircraft are needed in every field, and components made of thermoplastic composites are easy to produce, low-cost and durable.
Conventional aircraft. The next generation of conventional aircraft (mainly the new generation of single channel narrow body civil airliner) needs to give priority to reducing emissions and fuel costs, while taking into account the reduction of manufacturing costs. It needs to use materials that can reduce weight, be economical, easy to recycle and ensure quality.
Consumable aircraft. Expendable aircraft is the strategic development focus in the field of national defense. Such aircraft are often unmanned, designed to assist manned aircraft in performing risky missions and avoiding personal risks. Therefore, such products need to be manufactured to pay attention to cost-effectiveness, so that they can be sacrificed while saving the lives of pilots without causing large economic losses.
Urban air traffic and other emerging markets. Some emerging markets, such as urban air traffic aircraft, will be very different from the way aircraft are manufactured and produced today. The development of thermoplastic composites and related technology can assist its rapid turnover and realize the mass manufacturing of this kind of aircraft.
How can the properties of thermoplastic composites meet the project requirements?
It takes years of development to fully develop materials to make their performance meet equipment requirements. Mastering the professional knowledge required in the complex manufacturing process will make the whole industry face great challenges. Split has given priority to process improvement in the field of thermoplastic composite manufacturing. Through research and development, split is looking for creative ways to make thermoplastic composites more commonly used materials.
In addition, split is currently continuing to develop technologies related to thermoplastic composites to meet future application needs. Some of these features include:
Automatic fiber placement (AFP). As the largest user of automatic fiber placement machine in the world, split is applying this function to the high-speed laying of thermoplastic composite tow. This efficient manufacturing technology reduces costs and enables large-scale manufacturing to produce more cost-effective structures. The thermoplastic composite automatic fiber placement head recently purchased by split is * * * of similar products. This product shows that split uses its own technical expertise to improve the manufacturing capacity of thermoplastic composites.
Induction welding of thermoplastic composites uses coils and high-frequency alternating magnetic fields to induce eddy currents in conductive reinforcement materials to generate heat. Through this process, thermoplastic composite components are fused together under pressure to form an integrated "bonded" component without the need for additional materials, such as adhesives in the bonding layer. This technology reduces aircraft weight by connecting parts without fasteners and allows faster assembly and production of parts. Split demonstrated the aircraft front wheel Bay bulkhead assembly at the thermoplastic composites branch of the American composite Manufacturers Association (ACMA) in 2020. This component shows the manufacturing capacity of large-scale and complex geometry automatic fiber placement thermoplastic composites. At the same time, it also uses split's proprietary induction and resistance welding technology for assembly.

Large scale complex structure forming. In order to make full use of high-speed welding, components must be compatible with thermoplastic composites. Split is breaking through the limits of scale and complexity of traditional thermoplastic composite stamping, and exploring alternative methods for forming high aspect ratio parts with variable cross-section. The typical part of the complex stamping parts that split is developing is the fuselage frame part manufactured by using the layer decreasing and tow traction technology.
Today's aircraft is full of historical wisdom. Every machine, from military helicopters to commercial jets, is designed by the great minds in the industry. Thanks to innovative technologies such as thermoplastic composites, the current aircraft is trying to change the shape design to make it better and lighter than ever before. The story of thermoplastic composites in the aerospace field has just begun. At present, it still needs more sophisticated technology to make this material more common in the aerospace manufacturing field. In the current aircraft design and manufacturing process, split believes that it is time to give priority to the development of thermoplastic composites, so that the advanced functions and ideas of * * * generation aircraft can be realized.
Technical trends of six thermoplastic composites
Thermoplastic composites are increasingly used in aircraft and spacecraft to reduce weight, improve quality, and reduce manufacturing and maintenance costs.
1. use antibacterial plastic with stronger compatibility with disinfectant for aircraft interior
The cleaning and disinfection of aircraft interior surface can rapidly degrade traditional plastic materials.
***New antibacterial and disinfectant resistant plastics initially developed for hospital use are now being designated for aircraft interiors. These materials are formulated to meet the stringent flame, smoke, toxicity and heat release standards required by commercial aircraft.
2. select plastics that do not interfere with radio frequency (RF) signals for high-performance communication Radomes
The proliferation of unmanned aerial vehicles (UAVs), UAVs and satellites that rely on RF signals to control flight operations has increased the demand for highly reliable antennas*** The antenna function of the plastic radome requires that the RF signal will not be significantly attenuated within the required frequency and the operating temperature range of the whole equipment. Special engineering plastics with low dielectric constant, low dissipation coefficient, enhanced toughness, UV resistance and thermoformability are increasingly used to protect radomes.
3. specify high-strength thermoplastic composites to reduce weight and improve fuel efficiency
Aeronautical structures requiring high strength and stiffness are traditionally made of metal or thermosetting composites. However, these materials have some significant limitations. Metals are heavy, limiting their use in aerospace applications that require light weight. Thermosetting composites are often brittle and usually have poor chemical resistance. Thermosetting manufacturing is labor-intensive, and most thermosetting composites are not suitable for use at temperatures above 100 ℃.
The strength and modulus (hardness) values of a new kind of thermoplastic composites developed by ensinger company can be comparable with those of metals and thermosetting materials. This technology involves the insertion of continuous glass or carbon fibers into a thermoplastic polymer matrix, usually consisting of polyether ether ketone (PEEK) or ULTEM Pei (polyetherimide). Because the matrix is made of high-performance, heat stable plastics, these composites can be used at high temperatures.
Thermoplastic composites have many advantages related to thermoplastics, including ductility, fatigue resistance and shock absorption characteristics, as well as resistance to fuels, lubricants and cleaning chemicals. The plates made of these materials can be rapidly formed into finished parts using heated metal tools, which reduces the manufacturing cost.
4. select plastic with low flammability and high dielectric strength for electrical insulation
For a long time, plastics have been used in applications that require electrical insulation. The electrical system of modern military and civil aircraft may be particularly challenging, because in addition to good dielectric strength and arc resistance, Polymer Insulators must also be resistant to aircraft fuels and lubricants; Able to withstand vibration, wear and fatigue; And has excellent flammability. Plastic insulators on aircraft must also operate over a wide range of temperatures - from extreme cold at cruise altitude to extreme heat near jet engines.
Aircraft electrical system designers now specify the use of fluoropolymers such as polytetrafluoroethylene (PTFE), fluorinated ethylene propylene (FEP) and perfluoroalkoxyalkanes (PFA), as well as high-performance thermoplastics for demanding avionics applications, including support insulators, shrink tubes and flexible wire package insulation.
5. use innovative plastics to create * * * aircraft interior
Commercial airplanes are becoming more and more popular, and their interior decoration can be comparable to that of luxury hotel lobbies. Traditionally, the printing pattern of aircraft interior is problematic, because high flow areas are exposed to wear and repeated cleaning, which will quickly reduce the printing effect.
Newer technologies, such as the infusion imaging technology of Kydex thermoplastic, allow designers to create customized environments using images in materials rather than on materials.
Significant progress has also been made in managing plastic lens materials used to transmit light from commercial aircraft. The new polymer formula makes LED lamps have high transmittance, good diffusivity and accurate color control. Light management using high-performance plastics is having a positive impact on the aesthetics of aircraft interior space.
6. select durable high-temperature plastic to separate metal surfaces to improve reliability
Due to the inherent problems of paired metal surfaces subjected to vibration and / or sliding wear, the metal to metal connection is often the failure point of aircraft components. More and more designers use polyimide materials with good toughness and high performance for anti rotation elements such as spline couplings and locking fasteners to separate the application of metal parts. The introduction of polymer elements into components can extend the service life and the interval of required maintenance cycles.
For spline connections that transmit power to various aircraft systems through connected rotating metal axes, high-temperature couplings made of DuPont Vespel polyimide are installed between paired metal splines to achieve smoother operation and longer service life. When the rotating metal shaft is slightly misaligned, this method can reduce the wear of the spline. The ductility of the polymer allows misalignment of the shaft without undue stress on the metal shaft, bearing or drive motor.
In aviation locking fasteners, DuPont Vespel polyimide is used as a ductile locking element in nuts or bolts to prevent unnecessary rotation, without damaging the supporting metal fasteners during assembly or disassembly maintenance. This polymer element prevents seizing associated with the design of all metal locking fasteners.
In both cases, the polymer's ductility and wear properties mitigate the problems associated with metal to metal contact.
This article is reproduced from https://www.hongyantu.com/news/29275.html In case of infringement, please inform to delete
With the continuous exploration of materials, the market demand for thermoplastic composites is growing rapidly. ACMA has set up a composite growth group to promote and publicize thermoplastic composites to end users and thermosetting composite manufacturers, so as to make thermoplastic composites have more markets.
At the time of setting off the trend of thermoplastic composites abroad, the application of high-performance thermoplastic composites in the domestic market is still in a "placid" state, and neither the manufacturer nor the customer seems to have officially entered the state.
However, the application technology of thermoplastic composites in the aviation industry has been implemented.
Recently, we are delighted to welcome the successful completion of the first flight test of the first C919 large aircraft! It is reported that in the "skin" of C919, the consumption of the third generation aluminum lithium alloy materials and advanced composite materials reached 8.8% and 12% respectively. Compared with the "competitors" of Boeing 737 and Airbus A320, the C919 uses more advanced composite materials.
The birth of C919 marks that domestic large aircraft will soon enter the era of commercial operation. Let's look forward to the official delivery of domestic large aircraft, but also have more expectations for the application of advanced composite materials in aerospace.
Today, let's take a look at the outlook of international experts on the future application of thermoplastic composites in the aviation industry:
According to the 2022 issue on the website of spiritaerosystems, when you look at an airplane, what do you think of first? Advanced aviation equipment is a "time capsule", which carries the great ideas of a generation. So, when looking into the future of flight, what are the characteristics of this era that people hope the next generation of aircraft can show? Lighter, faster and more sustainable must be pursued continuously. The use of advanced structural thermoplastic composites is a solution for the new generation of aviation equipment to obtain these characteristics. However, due to the lack of appropriate equipment, opportunities and R & D priorities, thermoplastic composites can not give full play to their potential in the whole industry.
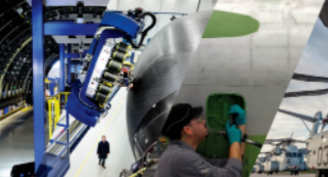
The development of next generation manufacturing processes, such as automatic forming, material placement and welding, must be industrialized so that thermoplastic composites can be widely used in large-scale aerospace manufacturing.
So why are thermoplastic composites important in aerospace? How will thermoplastic composites support the development of the next generation aircraft? How can the properties of thermoplastic composites meet the project requirements? What are the practical applications of advanced thermoplastic composites?
Why are thermoplastic composites important in aerospace?
Traditional metals such as aluminum and steel account for 70% of the materials used in aircraft manufacturing. However, the market demand for lighter and more efficient aircraft is increasing. In terms of thermosetting composites to reduce aircraft weight, researchers have rich professional knowledge. With the development of the industry, thermoplastic composites have gradually become the focus of research. Both types of materials use the high specific stiffness and strength of carbon fiber reinforced polymers to design lighter, higher strength aircraft.
At present, thermoplastic composites are replacing traditional materials in various applications, usually used in smaller parts. When thermoplastic composites are used in large components, such as longitudinal beams, frames, bulkheads and fuselage skin panels, the weight reduction effect of aviation equipment will be very significant, and the whole industry will also benefit greatly. Split's goal is to mature the use of thermoplastic composites in areas where automated high-speed manufacturing can be achieved, which means that the melting, forming and curing processes can be repeated in a very short period of time.
How will thermoplastic composites support the development of the next generation aircraft?
Thermoplastic composites have been clearly applied in three key fields: new generation conventional aircraft, consumable aircraft, urban air traffic (UAM) aircraft and other emerging markets. Light and high-performance aircraft are needed in every field, and components made of thermoplastic composites are easy to produce, low-cost and durable.
Conventional aircraft. The next generation of conventional aircraft (mainly the new generation of single channel narrow body civil airliner) needs to give priority to reducing emissions and fuel costs, while taking into account the reduction of manufacturing costs. It needs to use materials that can reduce weight, be economical, easy to recycle and ensure quality.
Consumable aircraft. Expendable aircraft is the strategic development focus in the field of national defense. Such aircraft are often unmanned, designed to assist manned aircraft in performing risky missions and avoiding personal risks. Therefore, such products need to be manufactured to pay attention to cost-effectiveness, so that they can be sacrificed while saving the lives of pilots without causing large economic losses.
Urban air traffic and other emerging markets. Some emerging markets, such as urban air traffic aircraft, will be very different from the way aircraft are manufactured and produced today. The development of thermoplastic composites and related technology can assist its rapid turnover and realize the mass manufacturing of this kind of aircraft.
How can the properties of thermoplastic composites meet the project requirements?
It takes years of development to fully develop materials to make their performance meet equipment requirements. Mastering the professional knowledge required in the complex manufacturing process will make the whole industry face great challenges. Split has given priority to process improvement in the field of thermoplastic composite manufacturing. Through research and development, split is looking for creative ways to make thermoplastic composites more commonly used materials.
In addition, split is currently continuing to develop technologies related to thermoplastic composites to meet future application needs. Some of these features include:
Automatic fiber placement (AFP). As the largest user of automatic fiber placement machine in the world, split is applying this function to the high-speed laying of thermoplastic composite tow. This efficient manufacturing technology reduces costs and enables large-scale manufacturing to produce more cost-effective structures. The thermoplastic composite automatic fiber placement head recently purchased by split is * * * of similar products. This product shows that split uses its own technical expertise to improve the manufacturing capacity of thermoplastic composites.
Induction welding of thermoplastic composites uses coils and high-frequency alternating magnetic fields to induce eddy currents in conductive reinforcement materials to generate heat. Through this process, thermoplastic composite components are fused together under pressure to form an integrated "bonded" component without the need for additional materials, such as adhesives in the bonding layer. This technology reduces aircraft weight by connecting parts without fasteners and allows faster assembly and production of parts. Split demonstrated the aircraft front wheel Bay bulkhead assembly at the thermoplastic composites branch of the American composite Manufacturers Association (ACMA) in 2020. This component shows the manufacturing capacity of large-scale and complex geometry automatic fiber placement thermoplastic composites. At the same time, it also uses split's proprietary induction and resistance welding technology for assembly.

Large scale complex structure forming. In order to make full use of high-speed welding, components must be compatible with thermoplastic composites. Split is breaking through the limits of scale and complexity of traditional thermoplastic composite stamping, and exploring alternative methods for forming high aspect ratio parts with variable cross-section. The typical part of the complex stamping parts that split is developing is the fuselage frame part manufactured by using the layer decreasing and tow traction technology.
Today's aircraft is full of historical wisdom. Every machine, from military helicopters to commercial jets, is designed by the great minds in the industry. Thanks to innovative technologies such as thermoplastic composites, the current aircraft is trying to change the shape design to make it better and lighter than ever before. The story of thermoplastic composites in the aerospace field has just begun. At present, it still needs more sophisticated technology to make this material more common in the aerospace manufacturing field. In the current aircraft design and manufacturing process, split believes that it is time to give priority to the development of thermoplastic composites, so that the advanced functions and ideas of * * * generation aircraft can be realized.
Technical trends of six thermoplastic composites
Thermoplastic composites are increasingly used in aircraft and spacecraft to reduce weight, improve quality, and reduce manufacturing and maintenance costs.
1. use antibacterial plastic with stronger compatibility with disinfectant for aircraft interior
The cleaning and disinfection of aircraft interior surface can rapidly degrade traditional plastic materials.
***New antibacterial and disinfectant resistant plastics initially developed for hospital use are now being designated for aircraft interiors. These materials are formulated to meet the stringent flame, smoke, toxicity and heat release standards required by commercial aircraft.
2. select plastics that do not interfere with radio frequency (RF) signals for high-performance communication Radomes
The proliferation of unmanned aerial vehicles (UAVs), UAVs and satellites that rely on RF signals to control flight operations has increased the demand for highly reliable antennas*** The antenna function of the plastic radome requires that the RF signal will not be significantly attenuated within the required frequency and the operating temperature range of the whole equipment. Special engineering plastics with low dielectric constant, low dissipation coefficient, enhanced toughness, UV resistance and thermoformability are increasingly used to protect radomes.
3. specify high-strength thermoplastic composites to reduce weight and improve fuel efficiency
Aeronautical structures requiring high strength and stiffness are traditionally made of metal or thermosetting composites. However, these materials have some significant limitations. Metals are heavy, limiting their use in aerospace applications that require light weight. Thermosetting composites are often brittle and usually have poor chemical resistance. Thermosetting manufacturing is labor-intensive, and most thermosetting composites are not suitable for use at temperatures above 100 ℃.
The strength and modulus (hardness) values of a new kind of thermoplastic composites developed by ensinger company can be comparable with those of metals and thermosetting materials. This technology involves the insertion of continuous glass or carbon fibers into a thermoplastic polymer matrix, usually consisting of polyether ether ketone (PEEK) or ULTEM Pei (polyetherimide). Because the matrix is made of high-performance, heat stable plastics, these composites can be used at high temperatures.
Thermoplastic composites have many advantages related to thermoplastics, including ductility, fatigue resistance and shock absorption characteristics, as well as resistance to fuels, lubricants and cleaning chemicals. The plates made of these materials can be rapidly formed into finished parts using heated metal tools, which reduces the manufacturing cost.
4. select plastic with low flammability and high dielectric strength for electrical insulation
For a long time, plastics have been used in applications that require electrical insulation. The electrical system of modern military and civil aircraft may be particularly challenging, because in addition to good dielectric strength and arc resistance, Polymer Insulators must also be resistant to aircraft fuels and lubricants; Able to withstand vibration, wear and fatigue; And has excellent flammability. Plastic insulators on aircraft must also operate over a wide range of temperatures - from extreme cold at cruise altitude to extreme heat near jet engines.
Aircraft electrical system designers now specify the use of fluoropolymers such as polytetrafluoroethylene (PTFE), fluorinated ethylene propylene (FEP) and perfluoroalkoxyalkanes (PFA), as well as high-performance thermoplastics for demanding avionics applications, including support insulators, shrink tubes and flexible wire package insulation.
5. use innovative plastics to create * * * aircraft interior
Commercial airplanes are becoming more and more popular, and their interior decoration can be comparable to that of luxury hotel lobbies. Traditionally, the printing pattern of aircraft interior is problematic, because high flow areas are exposed to wear and repeated cleaning, which will quickly reduce the printing effect.
Newer technologies, such as the infusion imaging technology of Kydex thermoplastic, allow designers to create customized environments using images in materials rather than on materials.
Significant progress has also been made in managing plastic lens materials used to transmit light from commercial aircraft. The new polymer formula makes LED lamps have high transmittance, good diffusivity and accurate color control. Light management using high-performance plastics is having a positive impact on the aesthetics of aircraft interior space.
6. select durable high-temperature plastic to separate metal surfaces to improve reliability
Due to the inherent problems of paired metal surfaces subjected to vibration and / or sliding wear, the metal to metal connection is often the failure point of aircraft components. More and more designers use polyimide materials with good toughness and high performance for anti rotation elements such as spline couplings and locking fasteners to separate the application of metal parts. The introduction of polymer elements into components can extend the service life and the interval of required maintenance cycles.
For spline connections that transmit power to various aircraft systems through connected rotating metal axes, high-temperature couplings made of DuPont Vespel polyimide are installed between paired metal splines to achieve smoother operation and longer service life. When the rotating metal shaft is slightly misaligned, this method can reduce the wear of the spline. The ductility of the polymer allows misalignment of the shaft without undue stress on the metal shaft, bearing or drive motor.
In aviation locking fasteners, DuPont Vespel polyimide is used as a ductile locking element in nuts or bolts to prevent unnecessary rotation, without damaging the supporting metal fasteners during assembly or disassembly maintenance. This polymer element prevents seizing associated with the design of all metal locking fasteners.
In both cases, the polymer's ductility and wear properties mitigate the problems associated with metal to metal contact.
This article is reproduced from https://www.hongyantu.com/news/29275.html In case of infringement, please inform to delete