Is the degradable plastic PBAT competitive?
China Petroleum and chemical industry, global polyurethane network / Xing Xiuyan / 2022-05-30 11:30:12 57770
Biodegradable plastics are considered to be an effective way to solve the problem of disposable plastic waste pollution. Biodegradable plastics include PLA (polylactic acid), PHA (polyhydroxyalkanoate), PBS polyester degradable plastics such as PBAT (polybutylene terephthalate), PBS (polybutylene succinate), PBSA (polybutylene succinate), PCL (polycaprolactone) and PGA (polyglycolic acid). It is estimated that by 2025, China's annual demand for degradable plastics will reach 3million tons / year. However, by then, China's degradable plastics production capacity will exceed 5million tons / year, of which PBAT alone will increase its planned production capacity by more than 3million tons. In the future, for the PBAT industry, who will the real competitiveness belong to?
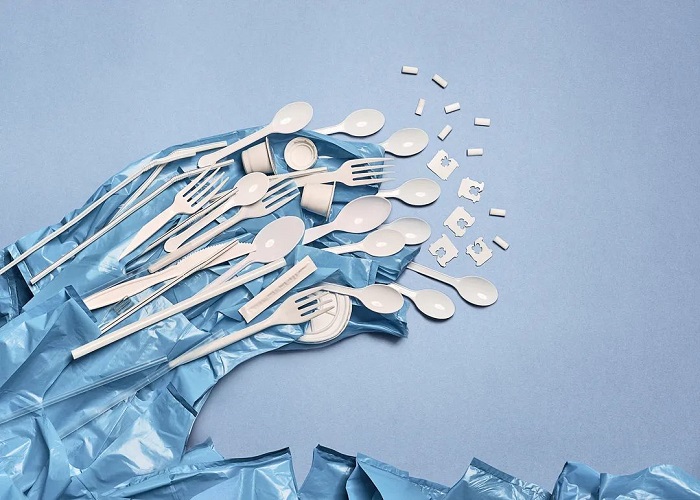
Degradable plastics in China
The annual global plastic output is as high as 350million tons, and China is close to 100million tons. Only 10% of disposable plastic products in the world are recycled every year, another 12% are burned, and more than 70% are discarded into the soil, air and sea. At present, most of the plastics produced are disposable plastics, about 40% of which are used for packaging, while polyethylene (PE), polyethylene terephthalate (PET), polypropylene (PP) and polystyrene (PS) are the most commonly used plastics in packaging. Once these petroleum derived plastics reach the environment, they will inevitably accumulate, resulting in negative environmental consequences.
Based on the protection of the common living environment of mankind, many countries have issued plastic restriction orders and plastic prohibition orders. China has also announced that by the end of 2020, the use of non degradable disposable plastic straws will be prohibited in the catering industry nationwide, and the use of non degradable disposable plastic straws will be prohibited in the catering industry serving food in the built-up areas of cities above the prefecture level; By the end of 2025, the use of non degradable disposable plastic tableware in the catering service in the built-up area of the county will be prohibited, and the non degradable disposable consumption intensity in the catering takeout field in cities above the prefecture level will be reduced by 30%.
Biodegradable plastics are considered to be an effective way to solve the problem of disposable plastic waste pollution. Biodegradable plastics include PLA, PHA, PBS polyester degradable plastics such as PBAT, PBS, PBSA, PCL and PGA.
in terms of demand, in 2020, Northeast Asia represented by China will be the world's largest biodegradable plastic market, accounting for more than 60% of global consumption, followed by Europe (25%) and North America (10%). In North America, the consumption of biodegradable plastics is expected to grow at an average annual rate of 6%. The food packaging, tableware, tableware and bag industries are the major end consumption of * * * and the main growth power of biodegradable plastic consumption. Benefiting from the global restrictions on plastic shopping bags and packaging, the world will achieve double-digit growth in the next few years.
In terms of supply, the output of biodegradable polymers in North America will increase to about 220000 tons in 2021. Polylactic acid is a large biodegradable plastic, accounting for 85% of the output; The output of Western Europe is 200000 tons, mostly from starch, PBAT and a small amount of PLA. However, degradable plastics in China have grown rapidly in recent years. According to incomplete statistics, the scale of China's degradable plastics industry has exceeded 1million tons / year, including PBAT, PLA, PPC, PGA, PBS, PHA and PCL. In terms of product scale, the PBAT industry has a large scale, with a total production capacity of nearly 800000 tons / year, followed by PLA, with a total production scale of more than 200000 tons / year. In 2021, China's output of degradable plastics will be about 800000 tons, basically balancing supply and demand.
China is the main battlefield of PBAT
It is estimated that by 2025, the demand for degradable plastics in China will reach 3million tons, but by then, the production capacity of degradable plastics in China will exceed 5million tons / year, of which PBAT alone will increase its planned production capacity by more than 3million tons / year, followed by the new production capacity from PLA and PGA.
PLA is an important sub industry in the field of bio based plastics and biodegradable products. As an ideal green polymer plastic, PLA has become the main product of biodegradable plastics. However, it is difficult for PLA to rapidly expand its short-term capacity to meet the growth of demand. The primary problem that puzzles the development of PLA industry in China is the synthesis technology of PLA intermediate product lactide. Anhui Fengyuan and Zhejiang Haizheng have gradually opened up the lactic acid lactide polylactic acid industrial chain and realized large-scale production, and developed more mature sets of process production equipment. At present, the total cost of producing PLA from lactide is more than 20000 yuan / ton, while the total cost of mastering lactide synthesis technology is about 15000 yuan / ton. However, China's corn and other crops have high economic value. With the global food crisis, it is difficult to enlarge the PLA industry in the short term from the perspective of cost economy and raw material availability.
PGA is an ideal fully biodegradable plastic, which has the characteristics of microbial degradation and water degradation. According to its molecular weight and degradation environment, it can be completely degraded within 1~6 months. It is non-toxic and harmless. The final degradation products of * * * are carbon dioxide and water. In addition to meeting the requirements of industrial composting, it can also meet the requirements of household composting, soil degradation and marine environment degradation. Several domestic enterprises have produced PGA from dimethyl oxalate (DMO), an important intermediate product of coal to ethylene glycol. Although the ethylene glycol market is depressed, enterprises can switch from ethylene glycol to PGA, and the full cost of PGA should be at least 12000 / ton, which does not include the loss of shutdown of ethylene glycol unit. The conversion from ethylene glycol to PGA will idle the ethylene glycol production unit, and the corresponding depreciation interest cost is not a decimal. However, if the new PGA is built from the coal head, the unit investment will be large, and the risk of higher coal prices will also be faced. The development path of PGA is very similar to that of coal to ethylene glycol. The capacity has been slowly expanded from 50000 tons to 200000 tons and 1million tons. However, it takes a long time to test the capacity expansion and the high quality to meet the demand.
PBAT shows good tensile strength, toughness, ductility and heat resistance, so it is one of the degradable plastics used in * * * in the market at present, and it is also the largest source of degradable plastics in China in the future. PBAT consumption in China is mainly used to produce starch containing compounds or mixed with PLA. The compound can greatly improve the tear strength and elongation of the finished product without affecting the later processing. These compounds can reduce the cost of products while still maintaining their biodegradable and compostable properties, and are further processed into shopping bags, rolled garbage bags, electronic product packaging bags, food packaging bags and mulch films.
Recently, major enterprises have launched PBAT, such as Hualu Hengsheng 30000 T / a PBAT, Donghua Tianye 400000 T / a PBAT, Dongfang Shenghong 180000 T / a PBAT, Yongrong holding 500000 T / a PBAT, Shaanxi coal group 120000 T / a PBAT and Huayi new material 300000 t / a PBAT. The planned PBAT capacity exceeds 3million tons.
PBAT is synthesized from BDO, PTA and adipic acid AA. From the availability and cost of raw materials, BDO is the key raw material for * * *. If the raw materials are calculated based on the outsourcing market price on May 20, 2022, the production of 1 ton of PBAT requires 0.54 tons of 1,4-butanediol BDO (22250 yuan / ton), 0.4 tons of adipic acid AA (11650 yuan / ton), 0.37 tons of PTA (6710 yuan / ton). The full cost of PBAT exceeds 22000 yuan / ton, while the market price of PBAT is about 21500 yuan / ton, which is a loss for enterprises relying solely on outsourcing.
In terms of production cost, BDO accounts for 63% of the three raw materials and 56% of PBAT's revenue. As adipic acid and PTA belong to large categories of products, with large industrial capacity and meager production profit, they can rely on outsourcing to meet the demand for raw materials. However, for BDO, if it completely relies on outsourcing, the production enterprise will have no profit. With the continuous expansion of PBAT capacity and the intensification of market competition, the price of PBAT appears or goes down. However, the price of BDO may go up further due to the demand of PBAT and traditional downstream spandex. For PBAT without BDO support, it will face the dilemma of continuous loss.

Those who win BDO win the world
In 2021, the domestic BDO production capacity is about 2.3 million tons, and the consumption is about 1.7 million tons. The downstream * * * major application is PTMEG spandex industrial chain, which accounts for more than 50%, followed by PBAT and lithium battery materials γ- Butyrolactone. From the demand side, the new production capacity of spandex is limited, which will only drive the consumption of 300000 tons of BDO in the next few years. However, for PBAT, one ton of PBAT will consume 0.54 tons of BDO. It is estimated that by 2025, China's demand for PBAT will be about 3.5 million tons, an increase of about 3million tons on the basis of 2020, which means that at least 1.6 million tons of BDO output will need to be increased to meet the demand for raw materials. Although there are a lot of BDO capacity planned in the near future, it is estimated that the actual production capacity will be less than 1.5 million tons by 2025, while the actual output is estimated to be less than 1million tons.
It is generally recognized in the industry that BDO is a major competitive weakness of * * *, so most PBAT planned capacity is equipped with BDO production lines to meet the raw material demand. However, we still face many insurmountable problems.
In terms of process, the technologies for BDO production include alkyne aldehyde method, maleic anhydride method, butadiene acetyl oxidation method, allyl alcohol method and dichlorobutene hydrolysis method. The latter three processes have the problems of large investment, many by-products and difficult production. Alkyne aldehyde method is a mature process for preparing bdo**** with acetylene and formaldehyde as raw materials; The sources of acetylene raw materials are divided into calcium carbide acetylene and natural gas acetylene, both of which are mature and applied process methods at present. However, the investment of butane maleic anhydride hydrogenation is large, and butane as the main raw material has a large external dependence.
Overseas, BDO is mainly produced through the natural gas to acetylene route. In China, the vast majority of BDO is based on carbide method. As an important clean energy, natural gas has many restrictions on the development of natural gas chemical industry, and few new natural gas acetylene BDO units are added; Under the double carbon policy, it is not easy to approve the new capacity of calcium carbide method. The production process of calcium carbide consumes a lot of electric energy. Calcium carbide is made from coal, and the approval of new coal chemical projects will be gradually tightened. For the production of BDO from calcium carbide, the full cost is about 13600 yuan / ton, and the full cost of integrated production of PBAT is 17600 yuan / ton. However, the author believes that in the future, with the continuous implementation of the double carbon policy, the production cost of calcium carbide will be further increased. In addition, the new batch capacity of calcium carbide is very limited, and the capacity will only increase from 40million tons / year in 2020 to 45million tons / year in 2025. However, assuming that the operating rate of 5million tons / year is 80%, the new output will be less than 4million tons / year, which can only meet the demand for new PVC (the demand for new PVC for calcium carbide is about 3.5 million tons / year). As mentioned above, a PBAT of 3million tons / year corresponds to a BDO production of 1.6 million tons / year, which translates into a demand of 1.8 million tons / year of calcium carbide (1.13 tons of calcium carbide is required to produce a ton of BDO), which also means that BDO has to compete with PVC for calcium carbide resources.
However, if BDO is prepared by n-butane maleic anhydride hydrogenation (1.14 tons of n-butane is required for the production of 1 ton of BDO), it needs to rely on external butane as raw material. In fact, it has natural advantages for propane dehydrogenation enterprises. Because according to the industry practice, PDH enterprises have to purchase butane while purchasing propane to reduce the overall logistics cost. For a long time, many PDH plants have been struggling with the deep processing of butane, and the strong demand for PBAT is making the prospect clearer. At present, although the price of butane is high, for the high price of BDO (22000 yuan / ton), the full cost of BDO produced by hydrogenation of butane maleic anhydride is close to 14000 yuan / ton, and the full cost of integrated production of PBAT is about 17800 yuan / ton. Compared with the market price of PBAT (21500 yuan / ton), the pre tax profit margin is still as high as 16%. However, butane was originally mainly used to be mixed with propane as fuel. With the intensification of the global energy crisis, butane gas will gradually rise. In addition, the demand for chemical industry continues to increase, such as propane butane cracking and PBAT. In the future, butane price will also gradually deviate from the fuel attribute.
In the future, for the PBAT industry, the real competitiveness belongs to the low-cost integrated BDO resources: first, there are supporting calcium carbide resources; The second is to obtain stable butane resources based on PDH unit. Only by developing PBAT based on resource advantages can we obtain strong enough market competitiveness.
This article is reproduced from https://www.hongyantu.com/news/29279.html In case of infringement, please inform to delete
Biodegradable plastics are considered to be an effective way to solve the problem of disposable plastic waste pollution. Biodegradable plastics include PLA (polylactic acid), PHA (polyhydroxyalkanoate), PBS polyester degradable plastics such as PBAT (polybutylene terephthalate), PBS (polybutylene succinate), PBSA (polybutylene succinate), PCL (polycaprolactone) and PGA (polyglycolic acid). It is estimated that by 2025, China's annual demand for degradable plastics will reach 3million tons / year. However, by then, China's degradable plastics production capacity will exceed 5million tons / year, of which PBAT alone will increase its planned production capacity by more than 3million tons. In the future, for the PBAT industry, who will the real competitiveness belong to?
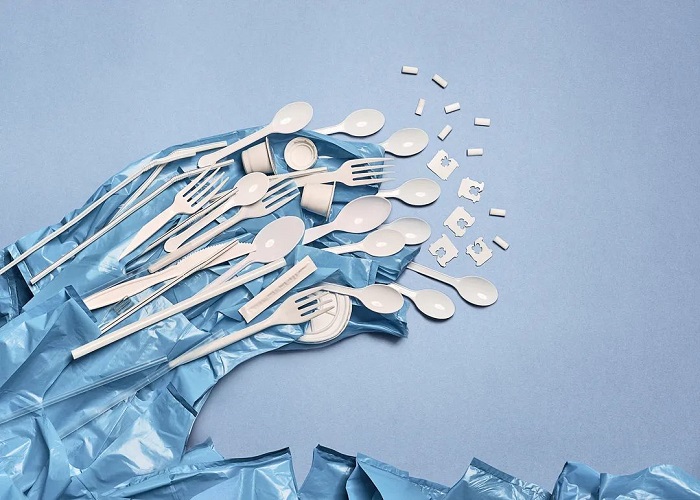
Degradable plastics in China
The annual global plastic output is as high as 350million tons, and China is close to 100million tons. Only 10% of disposable plastic products in the world are recycled every year, another 12% are burned, and more than 70% are discarded into the soil, air and sea. At present, most of the plastics produced are disposable plastics, about 40% of which are used for packaging, while polyethylene (PE), polyethylene terephthalate (PET), polypropylene (PP) and polystyrene (PS) are the most commonly used plastics in packaging. Once these petroleum derived plastics reach the environment, they will inevitably accumulate, resulting in negative environmental consequences.
Based on the protection of the common living environment of mankind, many countries have issued plastic restriction orders and plastic prohibition orders. China has also announced that by the end of 2020, the use of non degradable disposable plastic straws will be prohibited in the catering industry nationwide, and the use of non degradable disposable plastic straws will be prohibited in the catering industry serving food in the built-up areas of cities above the prefecture level; By the end of 2025, the use of non degradable disposable plastic tableware in the catering service in the built-up area of the county will be prohibited, and the non degradable disposable consumption intensity in the catering takeout field in cities above the prefecture level will be reduced by 30%.
Biodegradable plastics are considered to be an effective way to solve the problem of disposable plastic waste pollution. Biodegradable plastics include PLA, PHA, PBS polyester degradable plastics such as PBAT, PBS, PBSA, PCL and PGA.
in terms of demand, in 2020, Northeast Asia represented by China will be the world's largest biodegradable plastic market, accounting for more than 60% of global consumption, followed by Europe (25%) and North America (10%). In North America, the consumption of biodegradable plastics is expected to grow at an average annual rate of 6%. The food packaging, tableware, tableware and bag industries are the major end consumption of * * * and the main growth power of biodegradable plastic consumption. Benefiting from the global restrictions on plastic shopping bags and packaging, the world will achieve double-digit growth in the next few years.
In terms of supply, the output of biodegradable polymers in North America will increase to about 220000 tons in 2021. Polylactic acid is a large biodegradable plastic, accounting for 85% of the output; The output of Western Europe is 200000 tons, mostly from starch, PBAT and a small amount of PLA. However, degradable plastics in China have grown rapidly in recent years. According to incomplete statistics, the scale of China's degradable plastics industry has exceeded 1million tons / year, including PBAT, PLA, PPC, PGA, PBS, PHA and PCL. In terms of product scale, the PBAT industry has a large scale, with a total production capacity of nearly 800000 tons / year, followed by PLA, with a total production scale of more than 200000 tons / year. In 2021, China's output of degradable plastics will be about 800000 tons, basically balancing supply and demand.
China is the main battlefield of PBAT
It is estimated that by 2025, the demand for degradable plastics in China will reach 3million tons, but by then, the production capacity of degradable plastics in China will exceed 5million tons / year, of which PBAT alone will increase its planned production capacity by more than 3million tons / year, followed by the new production capacity from PLA and PGA.
PLA is an important sub industry in the field of bio based plastics and biodegradable products. As an ideal green polymer plastic, PLA has become the main product of biodegradable plastics. However, it is difficult for PLA to rapidly expand its short-term capacity to meet the growth of demand. The primary problem that puzzles the development of PLA industry in China is the synthesis technology of PLA intermediate product lactide. Anhui Fengyuan and Zhejiang Haizheng have gradually opened up the lactic acid lactide polylactic acid industrial chain and realized large-scale production, and developed more mature sets of process production equipment. At present, the total cost of producing PLA from lactide is more than 20000 yuan / ton, while the total cost of mastering lactide synthesis technology is about 15000 yuan / ton. However, China's corn and other crops have high economic value. With the global food crisis, it is difficult to enlarge the PLA industry in the short term from the perspective of cost economy and raw material availability.
PGA is an ideal fully biodegradable plastic, which has the characteristics of microbial degradation and water degradation. According to its molecular weight and degradation environment, it can be completely degraded within 1~6 months. It is non-toxic and harmless. The final degradation products of * * * are carbon dioxide and water. In addition to meeting the requirements of industrial composting, it can also meet the requirements of household composting, soil degradation and marine environment degradation. Several domestic enterprises have produced PGA from dimethyl oxalate (DMO), an important intermediate product of coal to ethylene glycol. Although the ethylene glycol market is depressed, enterprises can switch from ethylene glycol to PGA, and the full cost of PGA should be at least 12000 / ton, which does not include the loss of shutdown of ethylene glycol unit. The conversion from ethylene glycol to PGA will idle the ethylene glycol production unit, and the corresponding depreciation interest cost is not a decimal. However, if the new PGA is built from the coal head, the unit investment will be large, and the risk of higher coal prices will also be faced. The development path of PGA is very similar to that of coal to ethylene glycol. The capacity has been slowly expanded from 50000 tons to 200000 tons and 1million tons. However, it takes a long time to test the capacity expansion and the high quality to meet the demand.
PBAT shows good tensile strength, toughness, ductility and heat resistance, so it is one of the degradable plastics used in * * * in the market at present, and it is also the largest source of degradable plastics in China in the future. PBAT consumption in China is mainly used to produce starch containing compounds or mixed with PLA. The compound can greatly improve the tear strength and elongation of the finished product without affecting the later processing. These compounds can reduce the cost of products while still maintaining their biodegradable and compostable properties, and are further processed into shopping bags, rolled garbage bags, electronic product packaging bags, food packaging bags and mulch films.
Recently, major enterprises have launched PBAT, such as Hualu Hengsheng 30000 T / a PBAT, Donghua Tianye 400000 T / a PBAT, Dongfang Shenghong 180000 T / a PBAT, Yongrong holding 500000 T / a PBAT, Shaanxi coal group 120000 T / a PBAT and Huayi new material 300000 t / a PBAT. The planned PBAT capacity exceeds 3million tons.
PBAT is synthesized from BDO, PTA and adipic acid AA. From the availability and cost of raw materials, BDO is the key raw material for * * *. If the raw materials are calculated based on the outsourcing market price on May 20, 2022, the production of 1 ton of PBAT requires 0.54 tons of 1,4-butanediol BDO (22250 yuan / ton), 0.4 tons of adipic acid AA (11650 yuan / ton), 0.37 tons of PTA (6710 yuan / ton). The full cost of PBAT exceeds 22000 yuan / ton, while the market price of PBAT is about 21500 yuan / ton, which is a loss for enterprises relying solely on outsourcing.
In terms of production cost, BDO accounts for 63% of the three raw materials and 56% of PBAT's revenue. As adipic acid and PTA belong to large categories of products, with large industrial capacity and meager production profit, they can rely on outsourcing to meet the demand for raw materials. However, for BDO, if it completely relies on outsourcing, the production enterprise will have no profit. With the continuous expansion of PBAT capacity and the intensification of market competition, the price of PBAT appears or goes down. However, the price of BDO may go up further due to the demand of PBAT and traditional downstream spandex. For PBAT without BDO support, it will face the dilemma of continuous loss.

Those who win BDO win the world
In 2021, the domestic BDO production capacity is about 2.3 million tons, and the consumption is about 1.7 million tons. The downstream * * * major application is PTMEG spandex industrial chain, which accounts for more than 50%, followed by PBAT and lithium battery materials γ- Butyrolactone. From the demand side, the new production capacity of spandex is limited, which will only drive the consumption of 300000 tons of BDO in the next few years. However, for PBAT, one ton of PBAT will consume 0.54 tons of BDO. It is estimated that by 2025, China's demand for PBAT will be about 3.5 million tons, an increase of about 3million tons on the basis of 2020, which means that at least 1.6 million tons of BDO output will need to be increased to meet the demand for raw materials. Although there are a lot of BDO capacity planned in the near future, it is estimated that the actual production capacity will be less than 1.5 million tons by 2025, while the actual output is estimated to be less than 1million tons.
It is generally recognized in the industry that BDO is a major competitive weakness of * * *, so most PBAT planned capacity is equipped with BDO production lines to meet the raw material demand. However, we still face many insurmountable problems.
In terms of process, the technologies for BDO production include alkyne aldehyde method, maleic anhydride method, butadiene acetyl oxidation method, allyl alcohol method and dichlorobutene hydrolysis method. The latter three processes have the problems of large investment, many by-products and difficult production. Alkyne aldehyde method is a mature process for preparing bdo**** with acetylene and formaldehyde as raw materials; The sources of acetylene raw materials are divided into calcium carbide acetylene and natural gas acetylene, both of which are mature and applied process methods at present. However, the investment of butane maleic anhydride hydrogenation is large, and butane as the main raw material has a large external dependence.
Overseas, BDO is mainly produced through the natural gas to acetylene route. In China, the vast majority of BDO is based on carbide method. As an important clean energy, natural gas has many restrictions on the development of natural gas chemical industry, and few new natural gas acetylene BDO units are added; Under the double carbon policy, it is not easy to approve the new capacity of calcium carbide method. The production process of calcium carbide consumes a lot of electric energy. Calcium carbide is made from coal, and the approval of new coal chemical projects will be gradually tightened. For the production of BDO from calcium carbide, the full cost is about 13600 yuan / ton, and the full cost of integrated production of PBAT is 17600 yuan / ton. However, the author believes that in the future, with the continuous implementation of the double carbon policy, the production cost of calcium carbide will be further increased. In addition, the new batch capacity of calcium carbide is very limited, and the capacity will only increase from 40million tons / year in 2020 to 45million tons / year in 2025. However, assuming that the operating rate of 5million tons / year is 80%, the new output will be less than 4million tons / year, which can only meet the demand for new PVC (the demand for new PVC for calcium carbide is about 3.5 million tons / year). As mentioned above, a PBAT of 3million tons / year corresponds to a BDO production of 1.6 million tons / year, which translates into a demand of 1.8 million tons / year of calcium carbide (1.13 tons of calcium carbide is required to produce a ton of BDO), which also means that BDO has to compete with PVC for calcium carbide resources.
However, if BDO is prepared by n-butane maleic anhydride hydrogenation (1.14 tons of n-butane is required for the production of 1 ton of BDO), it needs to rely on external butane as raw material. In fact, it has natural advantages for propane dehydrogenation enterprises. Because according to the industry practice, PDH enterprises have to purchase butane while purchasing propane to reduce the overall logistics cost. For a long time, many PDH plants have been struggling with the deep processing of butane, and the strong demand for PBAT is making the prospect clearer. At present, although the price of butane is high, for the high price of BDO (22000 yuan / ton), the full cost of BDO produced by hydrogenation of butane maleic anhydride is close to 14000 yuan / ton, and the full cost of integrated production of PBAT is about 17800 yuan / ton. Compared with the market price of PBAT (21500 yuan / ton), the pre tax profit margin is still as high as 16%. However, butane was originally mainly used to be mixed with propane as fuel. With the intensification of the global energy crisis, butane gas will gradually rise. In addition, the demand for chemical industry continues to increase, such as propane butane cracking and PBAT. In the future, butane price will also gradually deviate from the fuel attribute.
In the future, for the PBAT industry, the real competitiveness belongs to the low-cost integrated BDO resources: first, there are supporting calcium carbide resources; The second is to obtain stable butane resources based on PDH unit. Only by developing PBAT based on resource advantages can we obtain strong enough market competitiveness.
This article is reproduced from https://www.hongyantu.com/news/29279.html In case of infringement, please inform to delete